Graphene composites: introduction and market status
What are composite materials?
Composite materials (also referred to as composition materials, or simply composites) are materials formed by combining two or more materials with different properties to produce an end material with unique characteristics. These materials do not blend or dissolve together but remain distinct within the final composite structure. Composite materials can be made to be stronger, lighter or more durable than traditional materials due to properties they gain from combining their different components.
Most composites are made up of two materials - the matrix (or binder) surrounds a cluster of fibers or fragments of a stronger material (reinforcement). A common example of this structure is fiberglass, which was developed in the 1940’s to be the first modern composite and is still in widespread use. In fiberglass, fine fibers of glass, which are woven into a cloth of sorts, act as the reinforcement in a plastic or resin matrix.
While composite materials are not a new concept (for example, mud bricks, made from dried mud embedded with straw pieces, have been around for thousands of years), recent technologies have brought many new and exciting composites to existence. By careful selection of matrix and reinforcement (as well as the best manufacturing process to bring them together) it is possible to create significantly superior materials, with tailored properties for specific needs. Typical composite materials include composite building materials like cement and concrete, different metal composites, plastic composites and ceramic composites.
How are composite materials made?
The three main factors that help mold the end composite material are the matrix, reinforcement and manufacturing process. As matrix, many composites use resins, which are thermosetting or thermosoftening plastics (hence the name ‘reinforced plastics’ often given to them). These are polymers that hold the reinforcement together and help determine the physical properties of the end composite.
Thermosetting plastics begin as liquid but then harden with heat. They do not return to liquid state and so they are durable, even in extreme exposure to chemicals and wear. Thermosoftening plastics are hard at low temperatures and but soften with heat. They are less commonly used but possess interesting advantages like long shelf life of raw material and capacity for recycling. There are other matrix materials such as ceramics, carbon and metals that are used for specific purposes.
Reinforcement materials grow more varied with time and technology, but the most commonly used ones are still glass fibers. Advanced composites tend to favor carbon fibers as reinforcement, which are much stronger than glass fibers, but are also more expensive. Carbon fiber composites are strong and light, and are used in aircraft structures and sports gear (golf clubs and various rackets). They are also increasingly used to replace metals that replace human bones. Some polymers make good reinforcement materials, and help make composites that are strong and light.
The manufacturing process usually involves a mould, in which the reinforcement is first placed and then the semi-liquid matrix is sprayed or poured in to form the object. Moulding processes are traditionally done by hand, though machine processing is becoming more common. One of the new methods is called ‘pultrusion’ and is ideal for making products that are straight and have a constant cross section, like different kinds of beams. Products that of thin or complex shape (like curved panels) are built up by applying sheets of woven fiber reinforcement, saturated with matrix material, over a mould. Advanced composites (like those which are used in aircraft) are usually made from a honeycomb of plastic held between two sheets of carbon-fiber reinforced composite material, which results in high strength, low weight and bending stiffness.
Where can composites be found?
Composite materials have many obvious advantages, as they can be made to be lightweight, strong, corrosion and heat resistant, flexible, transparent and more according to specific needs. Composites are already used in many industries, like boats, aerospace, sports equipment (golf shafts, tennis rackets, surfboards, hockey sticks and more), Automotive components, wind turbine blades, body armour, building materials, bridges, medical utilities and others. Composite materials’ merits and potential assures ample research in the field which is hoped to bring future developments and implementations in additional markets.
Modern aviation is a specific example of an industry with complex needs and requirements, which benefits greatly from composite materials’ advantages. This industry raises demands of light and strong materials, that are also durable to heat and corrosion. It is no surprise, then, that many aircraft have wing and tail sections, as well as propellers and rotor blades made of composites, along with much of the internal structure.
What is graphene?
Graphene is a two-dimensional matrix of carbon atoms, arranged in a honeycomb lattice. A single square-meter sheet of graphene would weigh just 0.0077 grams but could support up to four kilograms. That means it is thin and lightweight but also incredibly strong. It also has a large surface area, great heat and electricity conductivity and a variety of additional incredible traits. This is probably why scientists and researchers call it “a miracle material†and predict it will revolutionize just about every industry known to man.
Graphene and composite materials
As was stated before, graphene has a myriad of unprecedented attributes, any number of which could potentially be used to make extraordinary composites. The presence of graphene can enhance the conductivity and strength of bulk materials and help create composites with superior qualities. Graphene can also be added to metals, polymers and ceramics to create composites that are conductive and resistant to heat and pressure.
Graphene composites have many potential applications, with much research going on to create unique and innovative materials. The applications seem endless, as one graphene-polymer proves to be light, flexible and an excellent electrical conductor, while another dioxide-graphene composite was found to be of interesting photocatalytic efficiencies, with many other possible coupling of materials to someday make all kinds of composites. The potential of graphene composites includes medical implants, engineering materials for aerospace and renewables and much more.
Further reading
- Graphene Supercapacitors
- Introduction to graphene
- Graphene company database
- How to invest in the graphene revolution
- The Graphene Handbook, our very own guide to the graphene market
Sparc Technologies receives USD$730,000 R&D tax refund
Sparc Technologies has secured AUD$1.12 million (around USD$730,000) in an R&D tax refund, under the Australian Government's R&D Tax Incentive, relating to the 2024 financial year.
It was stated that this financial boost comes as a recognition of Sparc’s commitment to advancing sustainable technologies in high-performance coatings and polymers. This refund will strengthen the company’s cash position thereby providing continued support for Sparc's investment in Sparc Hydrogen, ecosparc® field trials and its work developing graphene based additives for high performance coatings and polymers
New method enables materials that combine graphene and metals
Researchers from CNR-IOM, University of Milano-Bicocca, University of Trieste and University of Vienna have developed a method to create new materials that combine the extraordinary properties of single metal atoms with the robustness, flexibility, and versatility of graphene.
Co and Ni adatoms diffusing across the substrate surface before being incorporated in the growing edge of the Gr layer. Image from: Science Advances
The method involves the controlled deposition of metal atoms, such as cobalt, during the formation of the graphene layer on a nickel surface. Some of these atoms are incorporated into the carbon network of graphene, creating a material with exceptional properties of robustness, reactivity, and stability even under critical conditions.
HydroGraph announces breakthrough in sustainable plastic packaging research
HydroGraph Clean Power has announced a technological advancement in its sustainable plastic packaging research.
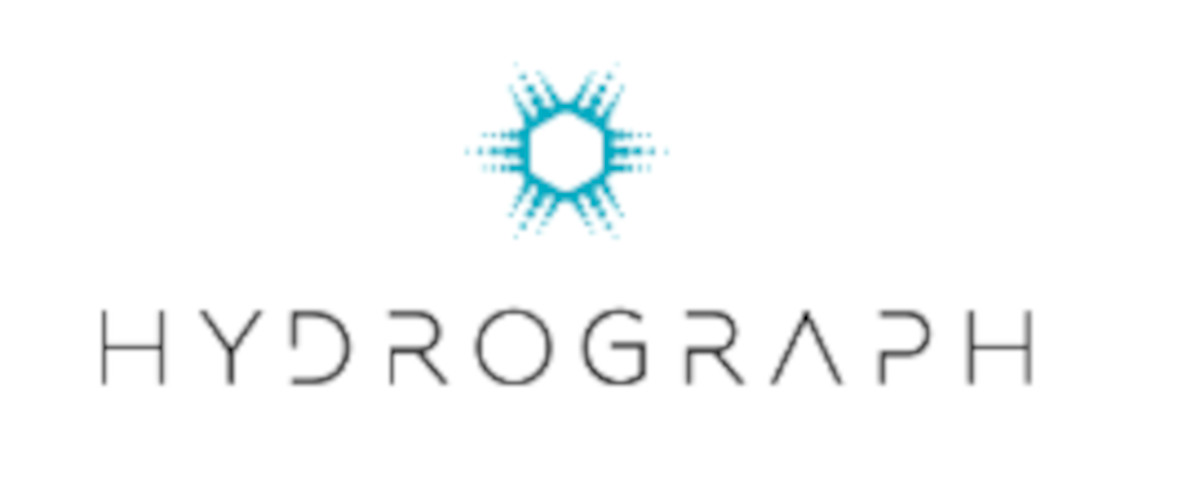
As the global polyethylene terephthalate (PET) packaging industry faces unprecedented regulatory pressure to reduce virgin plastic consumption, HydroGraph has found that its Fractal Graphene powder (FGA-1) can dramatically improve the performance and sustainability of PET bottles.
Researchers develop a new process for laser-induced graphene smart textile that could improve space gear
Researchers from the Korea Advanced Institute of Science and Technology (KAIST), Korea Institute of Machinery & Materials and Seoul National University of Science and Technology (SEOULTECH) have shown that laser-induced graphene (LIG), patterned with femtosecond laser pulses, can serve as a versatile material for temperature/strain sensing, stray light absorption, and heat management for smart spacesuits and telescopes.
Direct laser writing of laser-induced graphene (LIG). Image from: Advanced Functional Materials
The team has developed a manufacturing technique that addresses the challenges posed by the harsh conditions that space equipment must function in. The scientists' new process uses precisely controlled laser pulses to transform a Kevlar's surface into a porous graphene structure, effectively converting ordinary Kevlar fabric into a multifunctional material.
Art and science combine to create graphene-enhanced clay artwork
Researchers at the National University of Singapore (NUS), and Deliarts recently presented an interdisciplinary approach combining materials science, ultrasonication, artistic expression, and curatorial practice to develop graphene-enhanced ceramics, improving strength and aesthetics. The focus of the approach was incorporating graphene oxide (GO) into kaolin clay and exploring its effects on material properties.
Image taken from: technologynetworks.com, Credit: Daria Andreeva, National University of Singapore, and Delia Prvački, Deliarts Pte Ltd.
In recent years, scientists have been adding GO to ceramic slurries — consisting of particles of kaolin clay or other materials dispersed in water — to make fired ceramics more durable and resistant to thermal shock. The team adapted this technique by using ultrasound to better mix the GO into kaolin slurries. They adjusted GO concentration and ultrasound exposure time to find the conditions that most enhanced the resulting ceramics’ strength and heat resistance. The team also collaborated with artist-in-residence Delia Prvački, who created works from the new ceramic material that are on display at the National University of Singapore Museum.
Graphene oxide and chitosan sponge for ultrafast and precise recovery of gold from electronic waste
Researchers at the National University of Singapore, working with colleagues from Manchester University and Guangdong University of Technology, have developed a sponge-like material made of graphene oxide and chitosan, that can be used to extract gold from electronic waste. In their recent study, the research team describes how they made their sponge and how well it worked during testing.
Previous research has shown that removing gold, silver and other metals from electronic equipment that is no longer useful, as a way to recycle such materials, is a difficult task that often results in low yields and the generation of a variety of toxic pollutants. In this new work, the team has found a way to remove the gold in a way that is cheaper and cleaner than conventional methods and much more efficient as well.
Academia and private sector working together on graphene-enhanced aluminum composite cable technology for improved power lines
A research team consisting of private sector and academic partners and led by NETL (a U.S. Department of Energy national laboratory that drives innovation and delivers solutions for a clean and secure energy future) is working on a new ultra-conductive carbon (graphite and graphene) aluminum composite cable technology that could increase the electrical conductivity and strength of transmission cables leading to higher grid capacity and efficiency to accommodate future power generation demand.
In addition to NETL, the research team includes, Ohio University, MetalKraft Technologies, Frisk Alloy, Hydro Extensions, General Graphene Corporation and CONSOL Innovations.
Memsift Innovations acquires graphene membrane technology from Singapore’s Ngee Ann Polytechnic
Singapore-based Memsift Innovations has entered into a technology transfer agreement with Singapore’s Ngee Ann Polytechnic on an innovative graphene membrane technology.
It was explained that the technology, featuring graphene oxide-based hollow fiber ultrafiltration and nanofiltration membranes, was developed based on over a decade of research and development. The ultrafiltration technology utilizes a graphene oxide-block copolymer composite renowned for its exceptional chemical and thermal stability, making it ideal for harsh industrial applications. Its unique surface chemistry forms a protective water layer that effectively prevents fouling. The nanofiltration technology employs a robust single-layer modified graphene oxide membrane with synthetic water channels, enhancing selectivity and permeability. This enables efficient molecular-level separation and differentiation between monovalent and multivalent ions.
Graphmatech launches graphene composites to enhance hydrogen storage
Swedish startup Graphmatech has launched its AROS Polyamide-Graphene composites, which are reported to reduce hydrogen leakage by 83% compared to traditional commercial storage solutions. The graphene-enhanced material will be dedicated to hydrogen storage and transport applications. Graphmatech expects the solution to be implemented in approximately 1,000 light commercial vehicles (LCVs) and 500 heavy commercial vehicles by 2027.
The composite combines polyamide grades with graphene, “effectively blocking hydrogen from escaping while also making the plastic stronger”. Additionally, Graphmatech secured SEK 10 million (almost USD$949,000) from the Swedish Energy Agency to support the development and deployment of a modular mobile pilot-scale extrusion line for its polymer graphene materials designed for hydrogen applications.
Versarien updates on recent progress
Versarien has shared updates on its progress across several key sectors and markets, reporting a growing pipeline of opportunities, rising from £1.6 million (over USD$2 million) in October 2023 to £4.7 million currently (over USD$6,100,000), with £1.6 million (over USD$2 million) in commercial opportunities and £3.1 million (over USD$4 million) in grants. The Company said it continued to focus on developing advanced materials, especially graphene, through manufacturing-light operations and technology licensing.
In the construction sector, the company said it had placed orders for equipment to enhance its in-house construction testing capabilities following a July fundraising. The equipment would support the development of graphene-based products, such as Cementene. Versarien said it had also signed its first significant 3D construction printing (3DCP) contract with Building For Humanity CIC for a project in Accrington, UK. The Company anticipated on-site activities to begin in 2025.
Pagination
- Page 1
- Next page